“비가동시간, 너무 아깝지 않아?”
2019년 67,400대, 2020년 68,000대, 2021년 72,600대…
G2엔진 연간 생산대수다.
매해 증가하는 생산목표를 달성하려면 가공 라인의 ‘혁신’이 필요했다.
G2엔진 실린더 블록과 헤드를 생산하는 가공라인은 모두 자동으로 운영된다.
최소 인원이 현장의 자동화 흐름을 지켜보며 문제 상황을 해결하고 점검하는 방식이다.
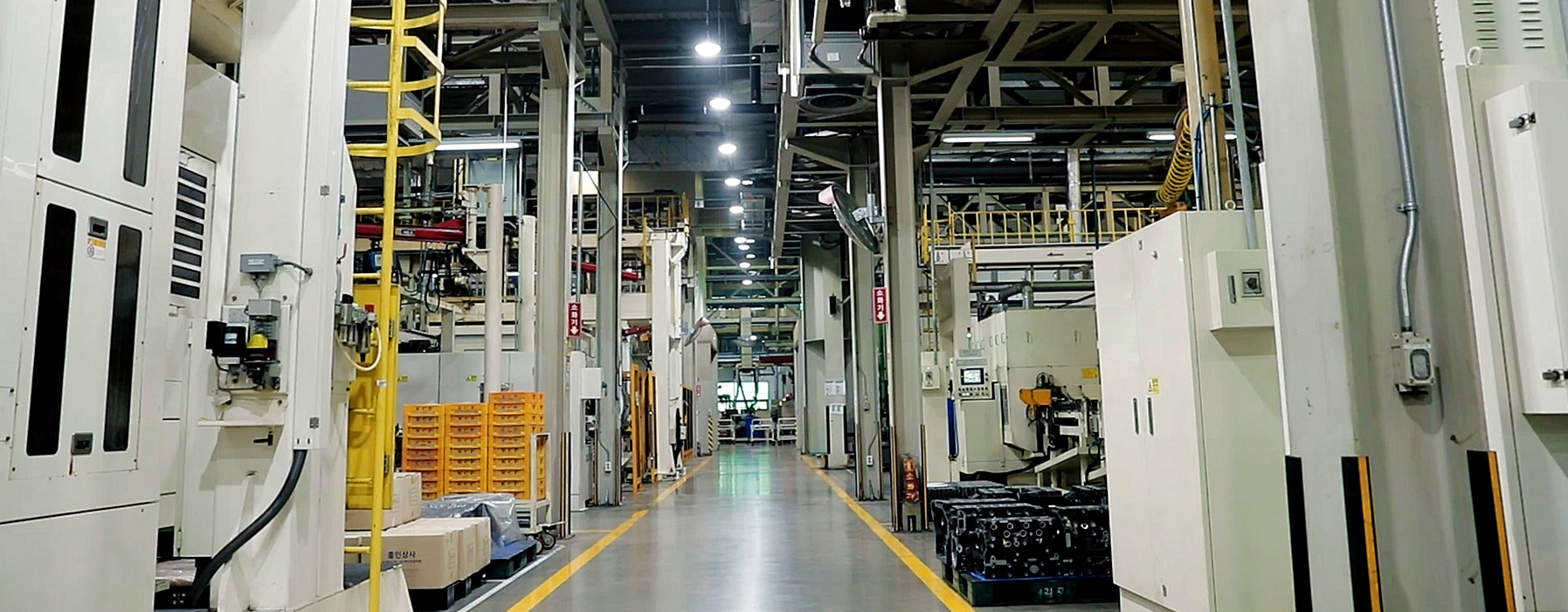
G2생산팀은 가공라인 생산량을 좌우하는 △가동시간 △가동률 △사이클 타임(Cycle Time)에 대한 고정관념을 깨보기로 했다. 여태 그렇게 해왔고, 당연하게 생각했던 ‘익숙함’에 대한 거부였다.
“현장 인원이 없을 때도 자동화 라인을 가동할 수는 없을까?”
“가동률을 방해하는 요인은 무엇일까?”
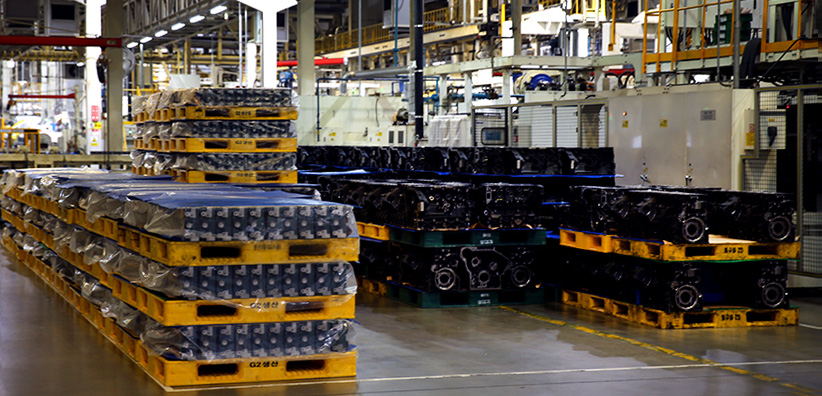
하루 중 G2엔진 가공라인이 멈추는 시간은 5.6시간.
현장 인원이 교대하고, 쉬고, 식사하는 시간이다. 이 시간들이 1년간 쌓이면, 56일이 넘는다.
이 중 절반만 라인을 가동해도 G2엔진 5,900대를 생산할 수 있는 어마어마한 시간이다.
‘이 시간에도 라인이 정상적으로 돌아갈 수 있는 환경을 만들어보면 어떨까?’
G2생산팀은 불가침 영역으로 생각했던 ‘비가동시간’을 바꿔보기로 했다.
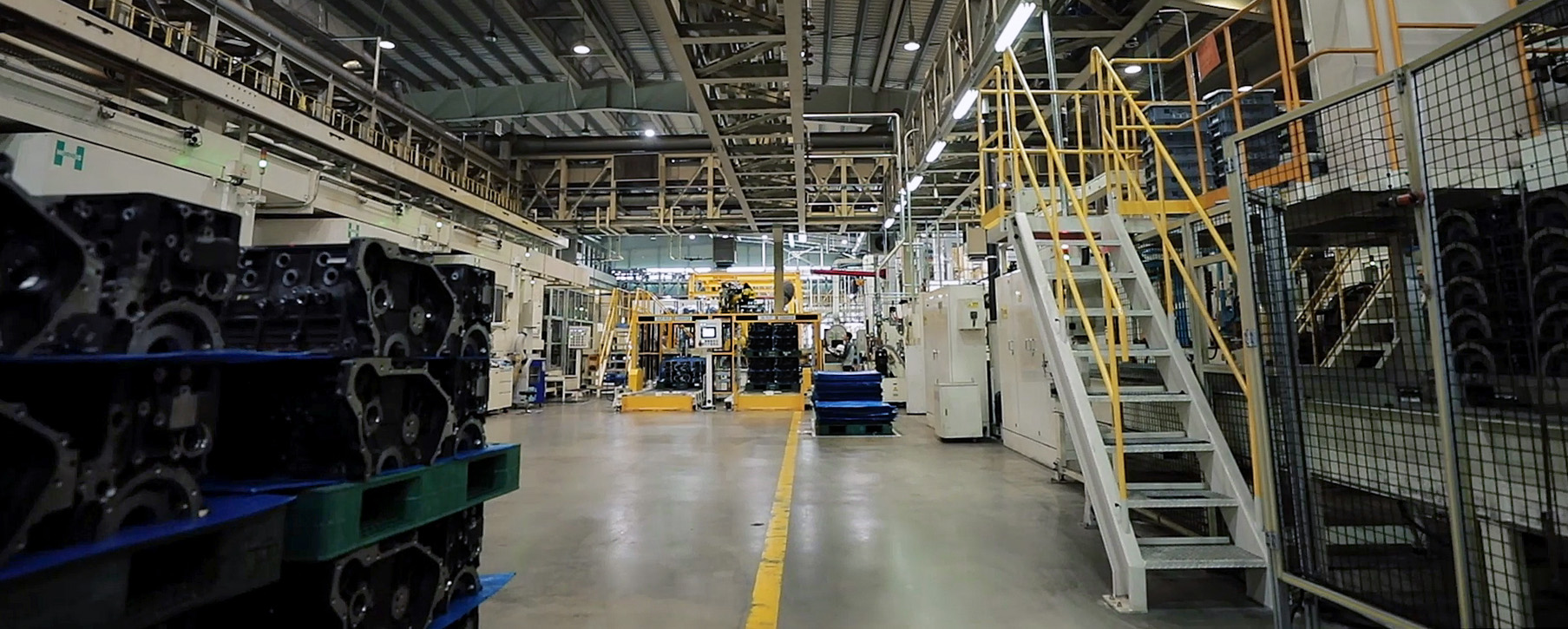
G2생산팀은 평소 라인 가동을 저해하는 요인을 찾기 시작했다.
평소에 설비 이상으로 가공 라인이 잠시 멈추거나 경고등이 울리는 상황을 관찰하고 정리했다.
공정 별로 연간 오류 내역과 개선 사항, 각종 비가동 사례도 취합했다.
취합된 오류 현상은 구조화했고, 아이템별로 개선 담당자도 정했다.
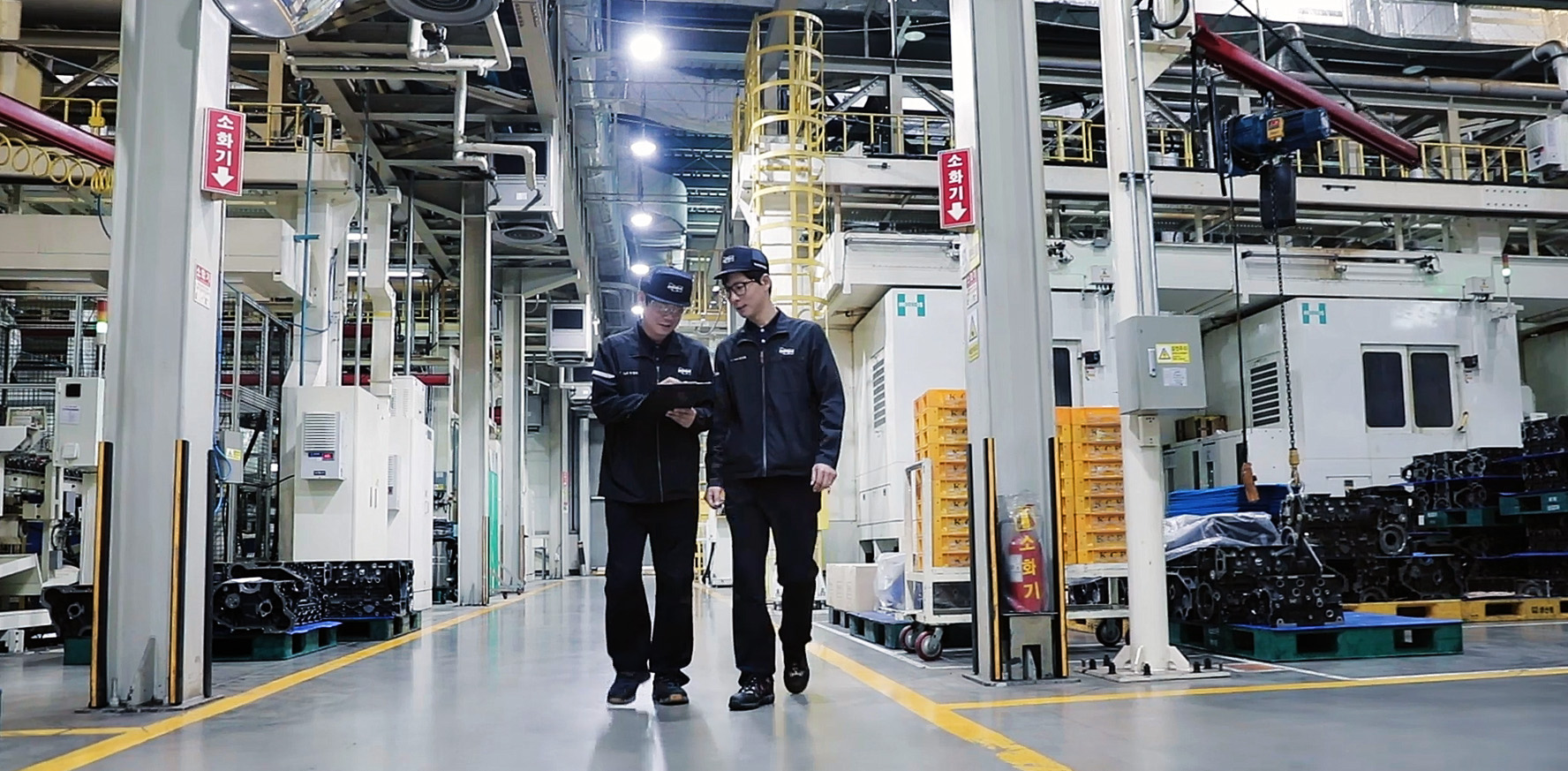
개선 담당자들은 설비 이상, 결품/불량 등 원인을 찾아 차근차근 문제를 개선해 나갔다.
예를 들어, 실린더 블록 헤드의 시리얼 넘버에 이물질만 묻어도 자동인식이 되지 않아 라인이 멈추는 문제가 있었다.
이 때마다 현장 근무자들이 이물질을 제거하고 라인을 재가동 시켰다.
“이물질 제거를 자동으로 해보자”
에어건 세척 공정을 도입해 봤다. 이후부터 시리얼 넘버 인식 오류로 라인이 서는 일은 사라졌다.
현장의 반발도 없진 않았다.
무인 가동을 위해선 ‘공구 교환’, ‘부품 준비’, ‘자주 검사’ 등 사전 추가 작업이 필요했다.
수작업으로 진행되는 최종 검사 파트에서는 특히 부담감을 가질 수밖에 없었다.
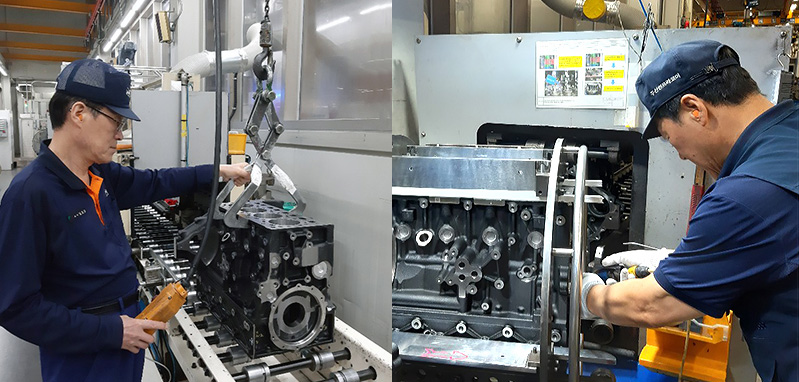
소통이 필요했다. G2생산팀 허명화 기장의 전폭적인 지원 아래 G2가공직 신철호 직장이 움직였다.
신 직장은 현장 인원들과 1:1 면담을 통해 개선 필요성을 설명하고 공감대를 형성했다.
권한과 책임도 반장들과 과감히 나눴다.
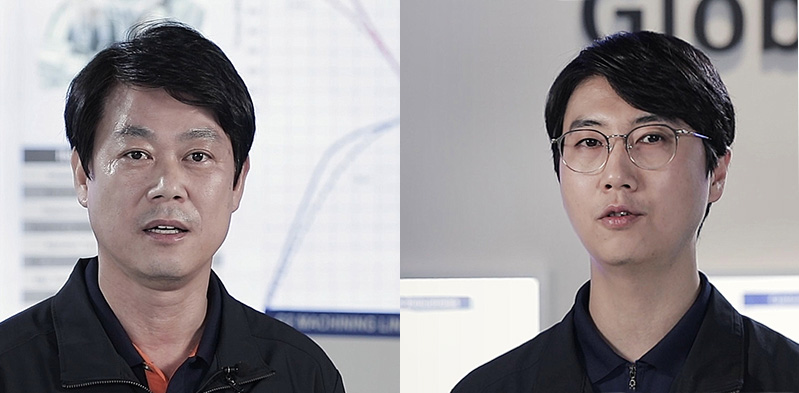
문제를 하나씩 해결할수록 자동화 흐름이 원활 해졌다.
설비 이상, 알람(Alarm)에 따른 부가 작업도 줄었다.
동료끼리 머리를 맞댈수록 라인 가동률이 높아졌고, 현장 인원들은 능동적으로 문제 상황을 찾아내고 개선하기 시작했다.
마침내 G2엔진 공장이 무인으로 가동되기 시작했다.
현장 인원이 없는 시간, 멈췄던 가공 라인이 무인으로 돌아가기 시작한 것.
무인 가동을 시작한 후, 2018년 한 해 블록 누적 가동률은 97.4%, 기존 대비 12.4%p나 향상됐다.
신철호 직장은 “G2생산팀 인원들의 적극적 개선이 없었다면 불가능한 일이었다”며 “모두가 회의적일때, 우리는 작은 성공의 경험들을 통해 성공을 확신했다”고 말했다.
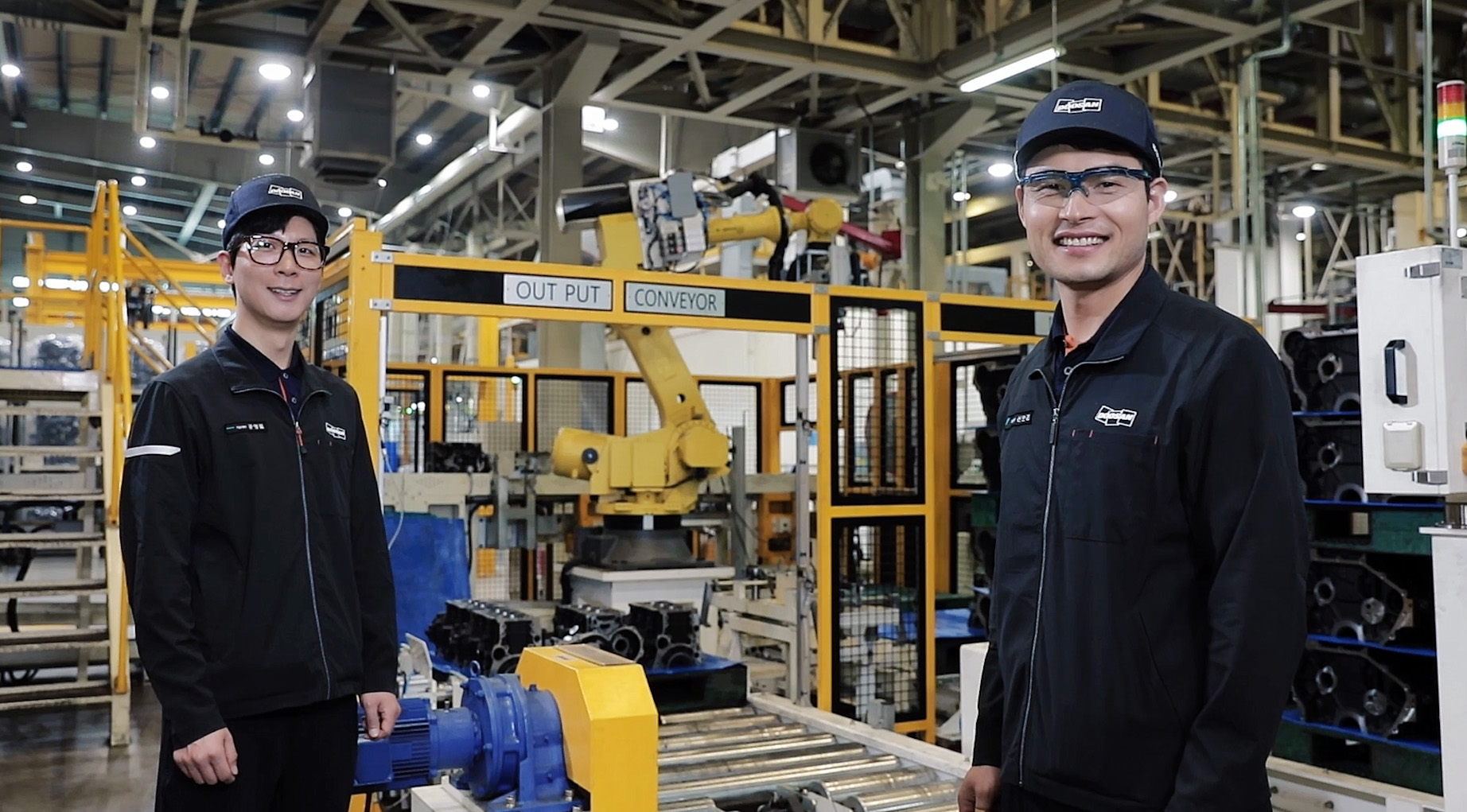
- G2생산팀 조상호 차장 인터뷰 중
‘혁신’은 새로운 비즈니스를 창출하거나 신기술을 개발해야만 하는 거창한 것이 아니다.
콜럼버스는 삶은 달걀을 세우기 위해 한 쪽 끝을 깨트렸다.
시작은 분명 어렵다. 하지만, ‘해보자’는 의지만 있다면 생각보다 단순할 수 있다.
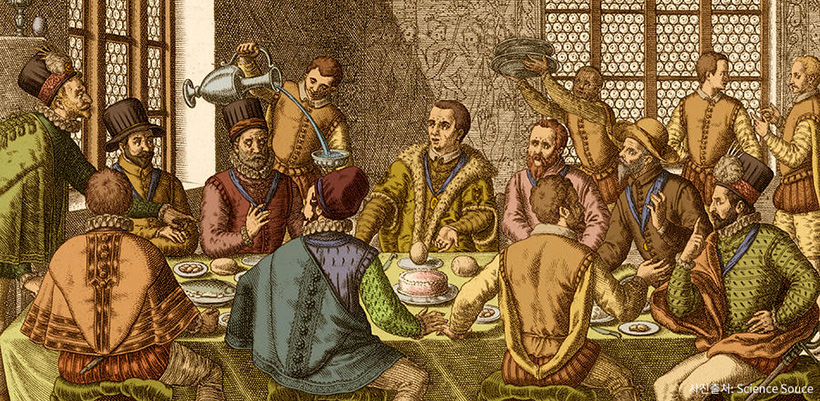
G2생산팀이 이뤄낸 ‘혁신’은 고정 관념을 다시 생각하고 바꿔 나간 ‘시도’의 결과였다.
생산 현장에서 발견한 ‘콜럼버스의 달걀’은 당연하고 사소한 것들을 뒤집어 새롭게 바라보는 것에서 시작됐다.
G2엔진 공장은 올해 5월, 헤드 6,800대, 블록 6,700대를 생산해내며 전례 없던 신기록을 달성했다.
혹자는 “나라를 구한다는 큰 포부로는 혁신을 꾀할 수 없다”고 했다.
일상의 불편함 하나만 없애보자는 작은 생각,
그리고 꾸준한 실천이 쌓일 때 우리는 혁신 기업으로 성장해 나갈 것이다.
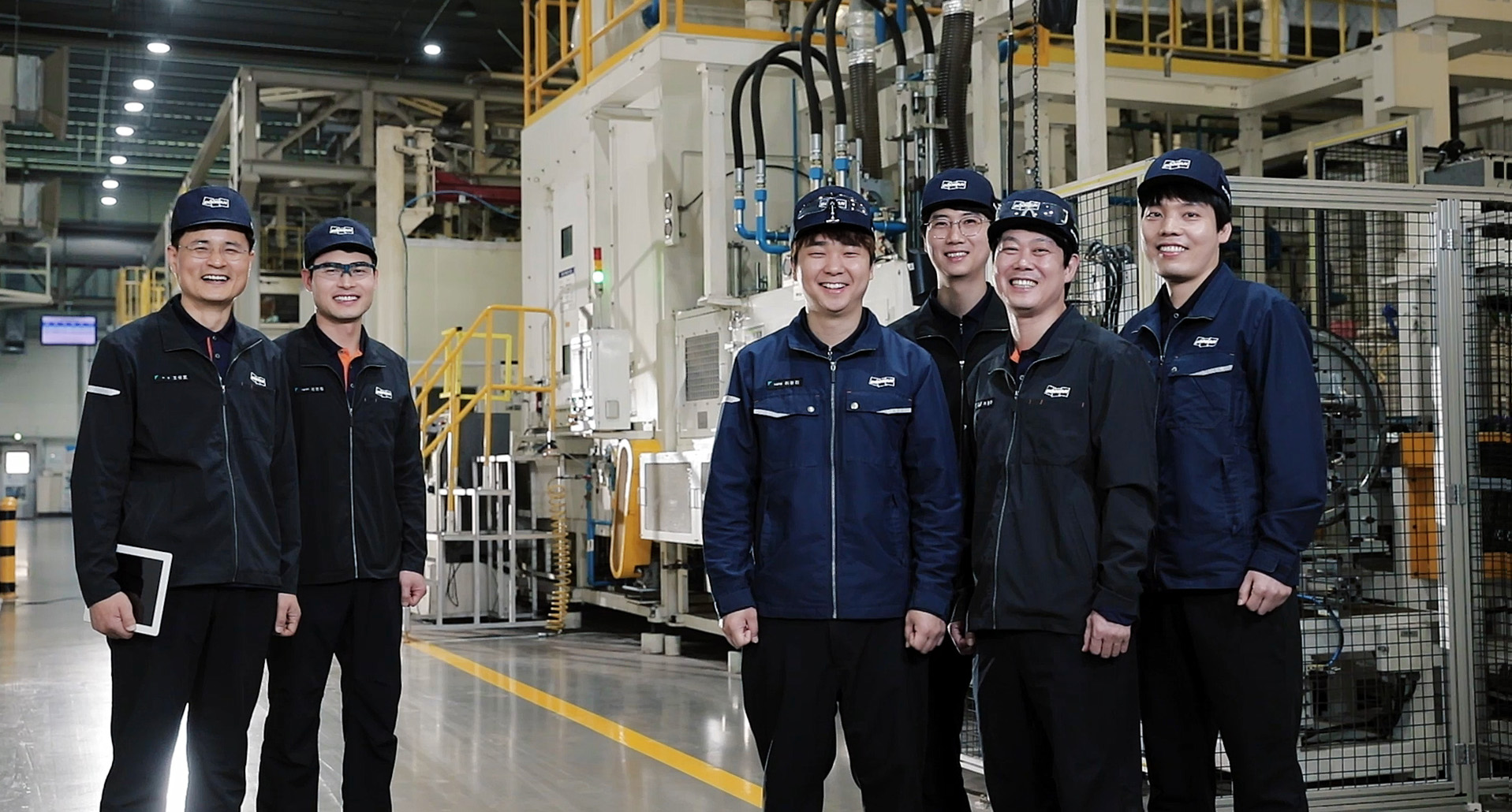
(사진 왼쪽부터) G2생산팀 조상호 차장, 선안진 반장, 이창진 반장, 신철호 직장, 허명화 기장, 엔진BG 생산기술팀 최현일 차장